પ્લાસ્ટિકના ભાગો કેવી રીતે ડિઝાઇન કરવા
ટૂંકું વર્ણન:
પ્રતિ પ્લાસ્ટિક ભાગો ડિઝાઇનભાગોના આકાર, કદ અને ચોકસાઈને નિર્ધારિત કરવાનું છે, ભાગોમાં ઉત્પાદનમાં ભૂમિકા અને પ્લાસ્ટિક માટે મોલ્ડિંગ પ્રક્રિયાના નિયમના આધારે. અંતિમ આઉટપુટ એ બીબામાં અને પ્લાસ્ટિકના ભાગના ઉત્પાદન માટેના રેખાંકનો છે.
ઉત્પાદન ઉત્પાદન ડિઝાઇનથી શરૂ થાય છે. પ્લાસ્ટિકના ભાગોની ડિઝાઇન સીધી ઉત્પાદનની આંતરિક રચના, કિંમત અને કાર્યની અનુભૂતિને નિર્ધારિત કરે છે, અને તે ઘાટનું ઉત્પાદન, કિંમત અને ચક્ર, તેમજ ઇન્જેક્શન મોલ્ડિંગ અને પોસ્ટ-પ્રોસેસિંગ પ્રક્રિયા અને ખર્ચનું આગલું પગલું પણ નક્કી કરે છે.
આધુનિક સમાજમાં વિવિધ ઉત્પાદનો, સુવિધાઓ અને લોકોના જીવનમાં પ્લાસ્ટિકના ભાગોનો વ્યાપકપણે ઉપયોગ થાય છે. પ્લાસ્ટિકના ભાગોને વિવિધ આકારો અને કાર્યોની જરૂર હોય છે. તેઓ પ્લાસ્ટિક સામગ્રીનો ઉપયોગ કરે છે અને તેમની ગુણધર્મો વૈવિધ્યસભર છે. તે જ સમયે, ઉદ્યોગમાં પ્લાસ્ટિકના ભાગો બનાવવાની ઘણી રીતો છે. તેથી પ્લાસ્ટિકના ભાગોની રચના કરવી એ સરળ કામ નથી.
વિવિધ ભાગ ડિઝાઇન અને સામગ્રી વિવિધ પ્રક્રિયા કરવામાં આવે છે. મોલ્ડિંગ પ્લાસ્ટિક માટેની પ્રક્રિયામાં મુખ્યત્વે નીચે શામેલ છે:
1. ઇંજેક્શન મોલ્ડિંગ
2. ફૂંકાતા મોલ્ડિંગ
3.com પ્રેશન મોલ્ડિંગ
4. પ્રોટોશનલ મોલ્ડિંગ
5.અથરમોફોર્મિંગ
6.Extrusion
7.ફ્રેબ્રિકેશન
8.ફોમિંગ
તેમને મોટા પ્રમાણમાં ઉત્પન્ન કરવાની ઘણી રીતો છે. ઇન્જેક્શન મોલ્ડિંગ એ લોકપ્રિય ઉત્પાદન પદ્ધતિ છે, કારણ કે ઇન્જેક્શન મોલ્ડેડ 50% ~ 60% પ્લાસ્ટિક ભાગો બાય ઈન્જેક્શન મોલ્ડિંગ દ્વારા બનાવવામાં આવે છે, તે એક ઉચ્ચ ગતિની ઉત્પાદન ક્ષમતા છે.
અમે ડિઝાઇન કરેલા કેટલાક પ્લાસ્ટિક ભાગો માટે કેસ બતાવો:
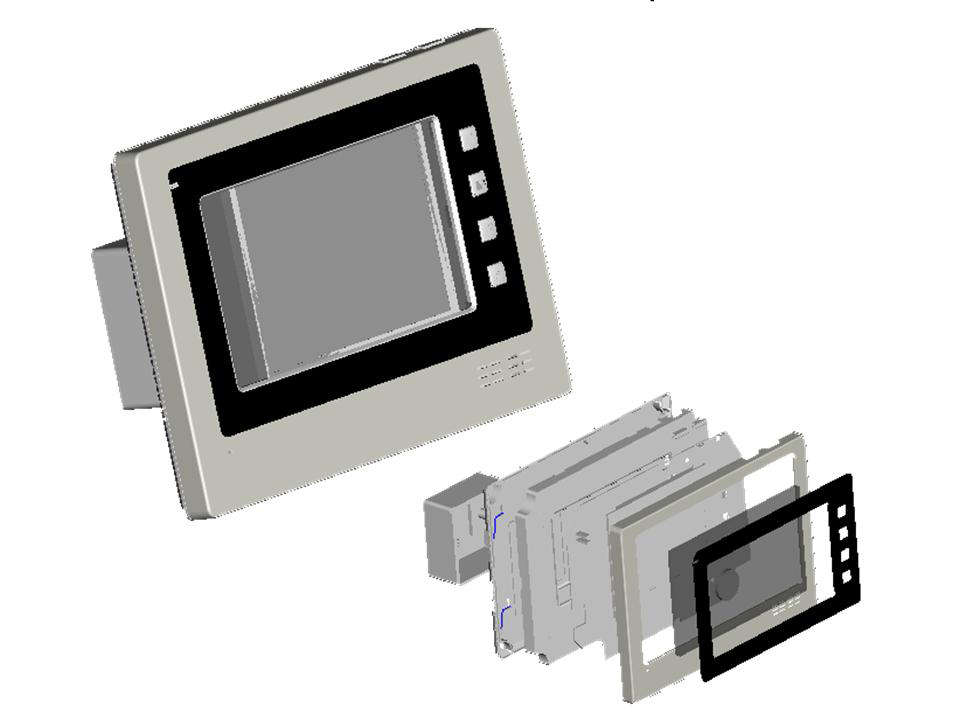
વિઝન ફોનનું પ્લાસ્ટિક બંધ
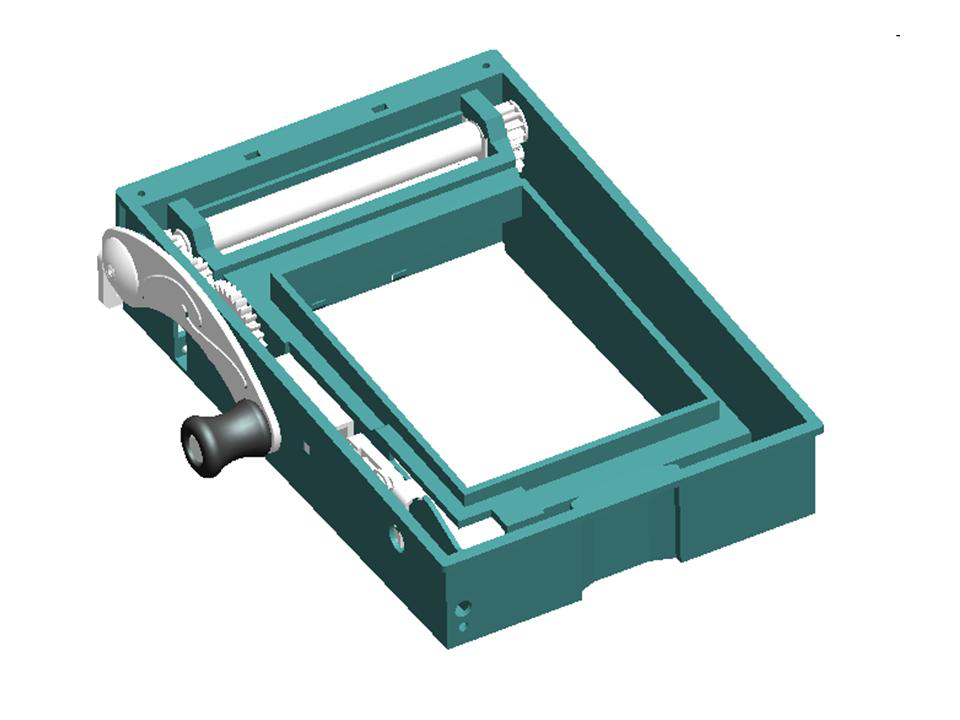
મિકેનિઝમના પ્લાસ્ટિક ભાગો
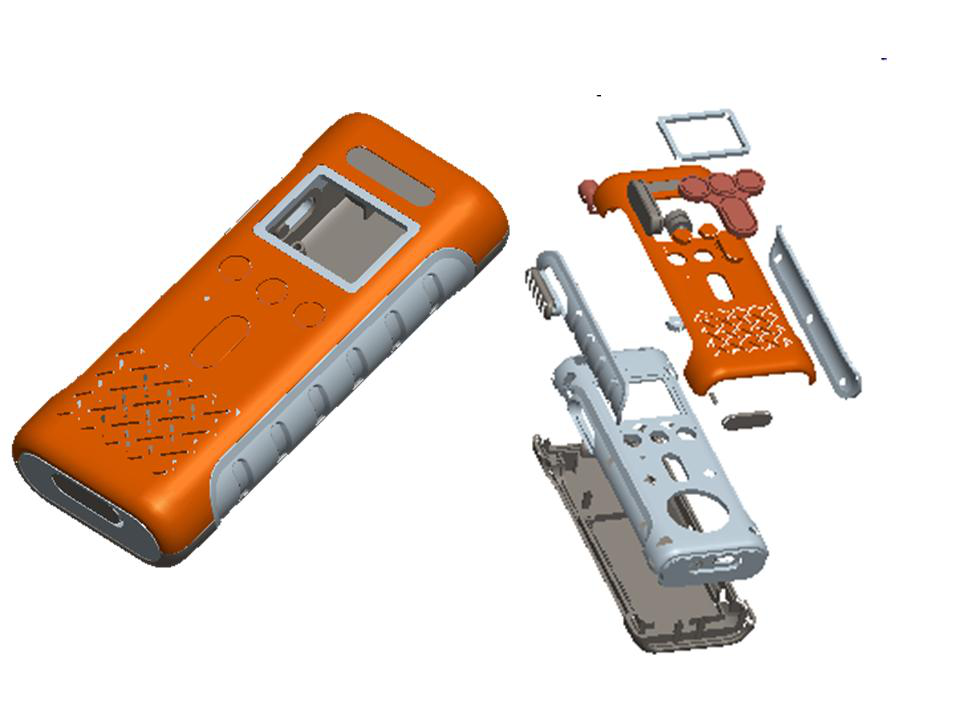
ઇલેક્ટ્રોનિકના પ્લાસ્ટિક કેસ
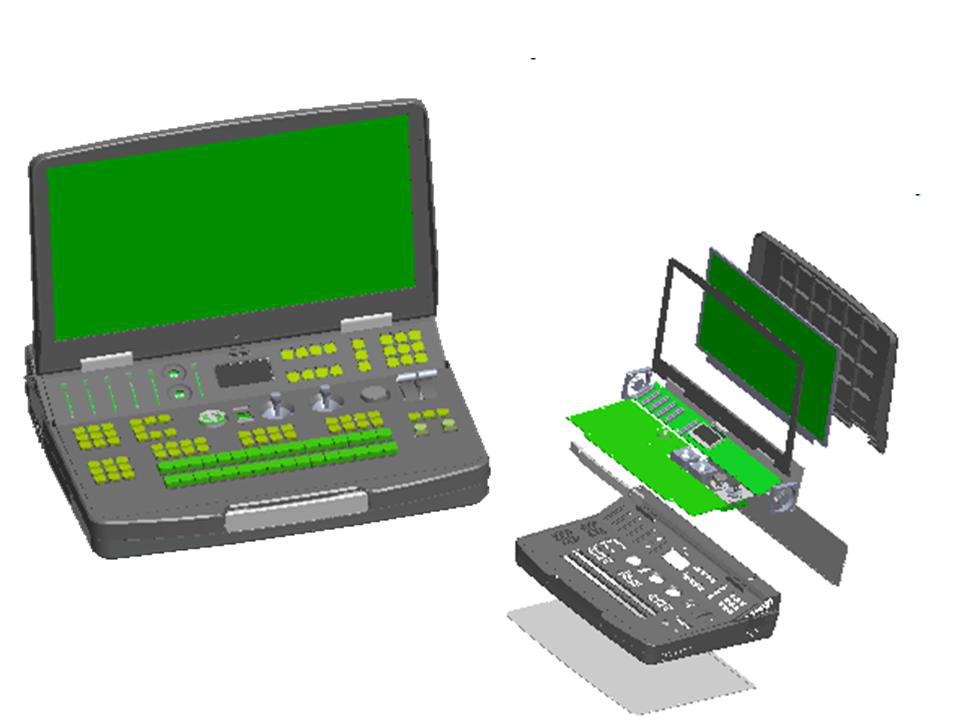
સાધન માટે પ્લાસ્ટિક આવાસો
નીચે આપણે ત્રણ બાબતોમાં પ્લાસ્ટિકના ભાગોને કેવી રીતે ડિઝાઇન કરવું તે વિગતવાર શેર કરીએ છીએ
પ્લાસ્ટિકના ભાગોને ડિઝાઇન કરવા માટેના 10 ટીપ્સ જે તમને ખબર હોવા જોઈએ
1. દેખાવની ડિઝાઇન અને ઉત્પાદનનું કદ નક્કી કરો.
આ ડિઝાઇનની આખી પ્રક્રિયામાં આ પહેલું પગલું છે. બજાર સંશોધન અને ગ્રાહકની આવશ્યકતાઓ અનુસાર ઉત્પાદનોનો દેખાવ અને કાર્ય નક્કી કરો અને ઉત્પાદન વિકાસ કાર્યો ઘડવો.
વિકાસ કાર્ય અનુસાર, વિકાસ ટીમ ઉત્પાદનને તકનીકી અને તકનીકી શક્યતા વિશ્લેષણ પર વહન કરે છે, અને ઉત્પાદનનું 3 ડી દેખાવ મોડેલ બનાવે છે. તે પછી, ફંકશન રીયલાઇઝેશન અને પ્રોડક્ટ એસેમ્બલી અનુસાર, શક્ય ભાગોની યોજના છે.
ઉત્પાદનના ડ્રોઇંગ્સમાંથી 2. વ્યક્તિગત ભાગોને અલગ કરો, પ્લાસ્ટિકના ભાગો માટે પ્લાસ્ટિક રેઝિન પ્રકાર પસંદ કરો
આ પગલું એ પાછલા પગલામાં મેળવેલા 3D મોડેલથી ભાગોને અલગ પાડવું અને તેમને વ્યક્તિગત રૂપે ડિઝાઇન કરવાનું છે. ભાગોની કાર્યાત્મક આવશ્યકતાઓ અનુસાર, પ્લાસ્ટિકની યોગ્ય કાચી સામગ્રી અથવા હાર્ડવેર સામગ્રી પસંદ કરો. ઉદાહરણ તરીકે, એબીએસ નો ઉપયોગ સામાન્ય રીતે
શેલ, એબીએસ / બીસી અથવા પીસીમાં અમુક યાંત્રિક ગુણધર્મો, પારદર્શક ભાગો જેવા કે લેમ્પશેડ, લેમ્પ પોસ્ટ પીએમએમએ અથવા પીસી, ગિયર અથવા પહેરવાના ભાગો પીઓએમ અથવા નાયલોન હોવું જરૂરી છે.
ભાગોની સામગ્રી પસંદ કર્યા પછી, વિગતવાર ડિઝાઇન શરૂ કરી શકાય છે.
3.ડિફાઈન ડ્રાફ્ટ એંગલ્સ
ડ્રાફ્ટ એંગલ્સ પ્લાસ્ટિકને ઘાટમાંથી દૂર કરવાની મંજૂરી આપે છે. ડ્રાફ્ટ એંગલ્સ વિના, ભાગ દૂર દરમિયાન ઘર્ષણને કારણે નોંધપાત્ર પ્રતિકાર આપશે. ડ્રાફ્ટ એંગલ્સ ભાગની અંદરની અને બહારની બાજુએ હોવા જોઈએ. Theંડા ભાગ, ડ્રાફ્ટ એંગલ મોટો. અંગૂઠાનો સરળ નિયમ એ છે કે ઇંચ દીઠ 1 ડિગ્રી ડ્રાફ્ટ એંગલ હોવો જોઈએ. પર્યાપ્ત ડ્રાફ્ટ એંગલ ન હોવાના પરિણામે ભાગની બાજુઓ અને / અથવા મોટા ઇજેક્ટર પિન માર્ક્સ (આ પછીથી વધુ) ની બાજુમાં સ્ક્રેપ્સ થઈ શકે છે.
બહારની સપાટીના ડ્રાફ્ટ એંગલ્સ: Theંડા ભાગ, ડ્રાફ્ટ એંગલ મોટો. અંગૂઠાનો સરળ નિયમ એ છે કે ઇંચ દીઠ 1 ડિગ્રી ડ્રાફ્ટ એંગલ હોવો જોઈએ. પર્યાપ્ત ડ્રાફ્ટ એંગલ ન હોવાના પરિણામે ભાગની બાજુઓ અને / અથવા મોટા ઇજેક્ટર પિન માર્ક્સ (આ પછીથી વધુ) ની બાજુમાં સ્ક્રેપ્સ થઈ શકે છે.
સામાન્ય રીતે, સારી દેખાવ સપાટી રાખવા માટે, ભાગોની સપાટી પર રચના બનાવવામાં આવે છે. ટેક્સચરવાળી દિવાલ રફ છે, ઘર્ષણ મોટી છે, અને તેને પોલાણમાંથી કા toવું સરળ નથી, તેથી તેને મોટા ડ્રોઇંગ એંગલની જરૂર છે. બરછટ પોત છે, મોટું ડ્રાફ્ટિંગ એંગલ આવશ્યક છે.
4. દીવાલની જાડાઈ / સમાન જાડાઈ
સોલિડ આકારનું મોલ્ડિંગ નીચેના કારણોને લીધે ઇંજેક્શન મોલ્ડિંગમાં ઇચ્છિત નથી.
1). કુલિંગ દિવાલની જાડાઈના ચોરસ પ્રમાણમાં છે. નક્કર માટે લાંબી ઠંડકનો સમય સામૂહિક ઉત્પાદનના અર્થતંત્રને પરાજિત કરશે. (ગરમીનો નબળો વાહક)
2) .ટિકર વિભાગ પાતળા વિભાગ કરતા વધુ સંકોચો, ત્યાં વિરોધી સંકોચન રજૂ કરે છે જેના પરિણામે વpageરપેજ અથવા સિંક માર્ક વગેરે આવે છે (પ્લાસ્ટિક અને પીવીટી લાક્ષણિકતાઓના સંકોચન લક્ષણો)
તેથી અમારી પાસે પ્લાસ્ટિકના ભાગની રચના માટે મૂળભૂત નિયમ છે; જ્યાં સુધી શક્ય હોય ત્યાં સુધી દિવાલની જાડાઈ એકસરખી હોવી જોઈએ અથવા ભાગની બહાર સતત હોવી જોઈએ. આ દિવાલની જાડાઈને નામની દિવાલની જાડાઈ કહેવામાં આવે છે.
જો ભાગમાં કોઈ નક્કર વિભાગ છે, તો તેને કોરની રજૂઆત કરીને હોલો બનાવવો જોઈએ. આ કોરની આસપાસ દિવાલની સમાન જાડાઈની ખાતરી કરવી જોઈએ.
3). દિવાલની જાડાઈ નક્કી કરવા માટે કયા વિચારણા છે?
તે કામ માટે ગા thick અને પૂરતા સખત હોવા જોઈએ. દિવાલની જાડાઈ 0.5 થી 5 મીમી હોઈ શકે છે.
તે ઝડપથી ઠંડુ થવા માટે પૂરતું પાતળું હોવું જોઈએ, પરિણામે નીચા ભાગનું વજન અને higherંચી ઉત્પાદકતા.
દિવાલની જાડાઈમાં કોઈપણ તફાવત શક્ય તેટલું ન્યૂનતમ રાખવું જોઈએ.
વિવિધ દિવાલની જાડાઈવાળા પ્લાસ્ટિકનો ભાગ વિવિધ ઠંડક દર અને વિવિધ સંકોચનનો અનુભવ કરશે. આવા કિસ્સામાં નજીકની સહનશીલતા પ્રાપ્ત કરવી ખૂબ મુશ્કેલ અને ઘણી વખત અશક્ય બની જાય છે. જ્યાં દિવાલની જાડાઈમાં વિવિધતા આવશ્યક છે, ત્યાં બંને વચ્ચેનું સંક્રમણ ક્રમિક હોવું જોઈએ.
5. ભાગો વચ્ચે જોડાણ ડિઝાઇન
સામાન્ય રીતે આપણે બે શેલ એક સાથે જોડવાની જરૂર છે. આંતરિક ઘટકો (પીસીબી એસેમ્બલી અથવા મિકેનિઝમ) મૂકવા માટે તેમની વચ્ચે બંધ ઓરડો બનાવવો.
સામાન્ય પ્રકારનાં જોડાણ:
1). સ્નેપ હૂક:
સ્નેપ હુક્સ કનેક્શન સામાન્ય રીતે નાના અને મધ્યમ કદના ઉત્પાદનોમાં વપરાય છે. તેની લાક્ષણિકતા એ છે કે ત્વરિત હૂક સામાન્ય રીતે ભાગોની ધાર પર સેટ કરવામાં આવે છે, અને ઉત્પાદનનું કદ નાનું કરી શકાય છે. જ્યારે એસેમ્બલ થાય છે, ત્યારે તે સ્ક્રુ ડ્રાઇવર, અલ્ટ્રાસોનિક વેલ્ડીંગ ડાઇ અને અન્ય જેવા કોઈપણ ઉપકરણોનો ઉપયોગ કર્યા વિના સીધા જ બંધ થાય છે. ગેરલાભ એ છે કે સ્નેપ હૂક્સ મોલ્ડને વધુ જટિલ બનાવી શકે છે. સ્નેપ હુક્સ કનેક્શનને ખ્યાલ આપવા અને બીબામાં ખર્ચ વધારવા માટે સ્લાઇડર મિકેનિઝમ અને લિફ્ટર મિકેનિઝમની જરૂર છે.
2). સ્ક્રુ સાંધા:
સ્ક્રુ સાંધા પે firmી અને વિશ્વસનીય છે. ખાસ કરીને, સ્ક્રુ + અખરોટનું ફિક્સેશન ખૂબ વિશ્વસનીય અને ટકાઉ છે, જે તિરાડો વિના બહુવિધ ડિસેમ્બલીઓને મંજૂરી આપે છે. સ્ક્રુ કનેક્શન મોટા લોકીંગ ફોર્સ અને મલ્ટીપલ ડિસમલિંગવાળા ઉત્પાદનો માટે યોગ્ય છે. ગેરલાભ એ છે કે સ્ક્રુ ક columnલમ વધુ જગ્યા લે છે.
3). માઉન્ટિંગ બોસ:
બોસ કનેક્શનને વધારવું એ બોસ અને છિદ્રો વચ્ચેના ચુસ્ત સંકલન દ્વારા બે ભાગોને ઠીક કરવાનું છે. ડિસએસેમ્બલ ઉત્પાદનોને મંજૂરી આપવા માટે કનેક્શનની આ રીત એટલી મજબૂત નથી. ગેરલાભ એ છે કે વિસ્થાપનનો સમય વધતાં લોકીંગની શક્તિમાં ઘટાડો થશે.
4). અલ્ટ્રાસોનિક વેલ્ડીંગ:
અલ્ટ્રાસોનિક વેલ્ડીંગ એ બે ભાગોને અલ્ટ્રાસોનિક મોલ્ડમાં મૂકીને અને સંપર્ક સપાટીને અલ્ટ્રાસોનિક વેલ્ડીંગ મશીનની ક્રિયા હેઠળ ફ્યુઝ કરીને છે. ઉત્પાદનનું કદ નાનું હોઇ શકે છે, ઇન્જેક્શન ઘાટ પ્રમાણમાં સરળ છે, અને કનેક્શન મક્કમ છે. ગેરલાભ એ અલ્ટ્રાસોનિક મોલ્ડ અને અલ્ટ્રાસોનિક વેલ્ડીંગ મશીનનો ઉપયોગ છે, ઉત્પાદનનું કદ ખૂબ મોટું હોઈ શકતું નથી. વિખેર્યા પછી, અલ્ટ્રાસોનિક ભાગો ફરીથી વાપરી શકાતા નથી.
6. અનડર્કટ્સ
અન્ડરકટ્સ એવી વસ્તુઓ છે જે બીબાના અડધા ભાગને દૂર કરવામાં દખલ કરે છે. અન્ડરકટ્સ ડિઝાઇનમાં ક્યાંય પણ દેખાઈ શકે છે. આ તેટલું જ અસ્વીકાર્ય છે, જો તે ભાગ પર ડ્રાફ્ટ એંગલના અભાવથી વધુ ખરાબ નથી. જો કે, કેટલાક અન્ડરકટ્સ આવશ્યક અને / અથવા અનિવાર્ય છે. તે કિસ્સાઓમાં, જરૂરી છે
અંડરકટ્સ બીબામાં ભાગો ખસેડીને / ખસેડીને ઉત્પન્ન થાય છે.
ધ્યાનમાં રાખો કે ઘાટ બનાવતી વખતે અન્ડરકટ્સ બનાવવી વધુ ખર્ચાળ હોય છે અને તેને ઓછામાં ઓછી રાખવી જોઈએ.
7. આધાર પાંસળી / ગુસેટ્સ
પ્લાસ્ટિકના ભાગમાં પાંસળી ભાગની જડતા (ભાર અને ભાગની અવધિ વચ્ચેનો સંબંધ) સુધારે છે અને કઠોરતામાં વધારો કરે છે. તે ઘાટની ક્ષમતામાં પણ વધારો કરે છે કારણ કે તેઓ પાંસળીની દિશામાં ઓગળેલા પ્રવાહમાં ઉતાવળ કરે છે.
પાંસળી એ ભાગની બિન-દેખાવ સપાટી પર મહત્તમ તાણ અને ડિફ્લેક્શનની દિશામાં મૂકવામાં આવે છે. ઘાટ ભરવા, સંકોચન અને ઇજેક્શનથી પણ પાંસળીના પ્લેસમેન્ટના નિર્ણયને પ્રભાવિત કરવો જોઈએ.
પાંસળી જે vertભી દિવાલ સાથે જોડાતી નથી તે અચાનક સમાપ્ત થવી જોઈએ નહીં. નજીવી દિવાલમાં ધીમે ધીમે સંક્રમણથી તાણની સાંદ્રતા માટેનું જોખમ ઓછું થવું જોઈએ.
પાંસળી - પરિમાણો
પાંસળી નીચેના પરિમાણો હોવા જોઈએ.
સિંક માર્ક ટાળવા માટે પાંસળીની જાડાઈ 0.5 થી 0.6 ગણી નજીવી દિવાલની જાડાઈ વચ્ચે હોવી જોઈએ.
પાંસળીની heightંચાઈ 2.5 થી 3 વખત નજીવી દિવાલની જાડાઈ હોવી જોઈએ.
ઇજેક્શન સરળ બનાવવા માટે પાંસળી પાસે 0.5 થી 1.5-ડિગ્રી ડ્રાફ્ટ એંગલ હોવો જોઈએ.
પાંસળીના પાયામાં 0.25 થી 0.4 ગણી ત્રિજ્યાની નજીવી દિવાલની જાડાઈ હોવી જોઈએ.
બે પાંસળી વચ્ચેનું અંતર 2 થી 3 વખત (અથવા વધુ) નજીવી દિવાલની જાડાઈ હોવું જોઈએ.
8. રેડિઓઝ્ડ એજ
જ્યારે બે સપાટીઓ મળે છે, ત્યારે તે એક ખૂણા બનાવે છે. ખૂણા પર, દિવાલની જાડાઈ નજીવી દિવાલની જાડાઈમાં 1.4 ગણો વધે છે. આ તફાવત સંકોચન અને મોલ્ડ-ઇન-સ્ટ્રેસ અને લાંબા સમય સુધી ઠંડક માટે પરિણમે છે. તેથી, તીક્ષ્ણ ખૂણા પર સેવામાં નિષ્ફળતાનું જોખમ વધે છે.
આ સમસ્યાને હલ કરવા માટે, ખૂણા ત્રિજ્યાથી સ્મૂથ કરવા જોઈએ. ત્રિજ્યા બાહ્ય તેમજ આંતરિક રીતે પ્રદાન કરવા જોઈએ. આંતરિક તીવ્ર ખૂણા ક્યારેય ન રાખો કારણ કે તે ક્રેકને પ્રોત્સાહન આપે છે. ત્રિજ્યા એવા હોવું જોઈએ કે જે તેઓ દિવાલની જાડાઈના નિયમની પુષ્ટિ કરે છે. ખૂણાઓ પર દિવાલની જાડાઈ 0.6 થી 0.75 ગણો ત્રિજ્યા હોવું વધુ સારું છે. આંતરિક તીવ્ર ખૂણા ક્યારેય ન રાખો કારણ કે તે ક્રેકને પ્રોત્સાહન આપે છે.
9.સ્ક્રુ બોસ ડિઝાઇન
અમે હંમેશા બે અડધા કેસને એક સાથે ઠીક કરવા માટે સ્ક્રૂનો ઉપયોગ કરીએ છીએ, અથવા પીસીબીએ અથવા અન્ય ઘટકો પ્લાસ્ટિકના ભાગો પર જોડવું. તેથી સ્ક્રુ બોસ એ સ્ક્રૂ કરવા અને નિશ્ચિત ભાગો માટેની રચના છે.
સ્ક્રુ બોસ આકારમાં નળાકાર છે. બોસ માતા ભાગ સાથે આધાર પર જોડાયેલ હોઈ શકે છે અથવા તે બાજુમાં જોડાયેલ હોઈ શકે છે. બાજુથી જોડાવાથી પ્લાસ્ટિકના જાડા ભાગમાં પરિણમી શકે છે, જે ઇચ્છનીય નથી કારણ કે તે સિંક માર્કનું કારણ બની શકે છે અને ઠંડકનો સમય વધારી શકે છે. સ્કેચમાં બતાવ્યા પ્રમાણે બાજુની દિવાલ સાથે પાંસળી દ્વારા બોસને જોડીને આ સમસ્યા ઉકેલી શકાય છે. બ buttટર્સ પાંસળી આપીને બોસને કઠોર બનાવી શકાય છે.
સ્ક્રુનો ઉપયોગ બોસ પર કેટલાક અન્ય ભાગને જોડવા માટે થાય છે. ત્યાં થ્રેડો બનાવતા પ્રકારનાં સ્ક્રૂ અને ટ્રેડ કટીંગ પ્રકારના સ્ક્રૂ છે. થ્રેડો બનાવતા સ્ક્રૂનો ઉપયોગ થર્મોપ્લાસ્ટિક્સ પર થાય છે અને થ્રેડ કટીંગ સ્ક્રૂનો ઉપયોગ બિનસલાહભર્યા થર્મોસેટ પ્લાસ્ટિક ભાગો પર થાય છે.
થ્રેડો બનાવતી સ્ક્રૂ ઠંડા પ્રવાહ દ્વારા બોસની આંતરિક દિવાલ પર સ્ત્રી થ્રેડો ઉત્પન્ન કરે છે - પ્લાસ્ટિક કાપવાને બદલે સ્થાનિક રીતે વિકૃત છે.
સ્ક્રુ બોસને સ્ક્રુ દાખલ કરવાના દળો અને સેવામાં સ્ક્રુ પર મૂકવામાં આવેલા ભારને ટકી રહેવા માટે યોગ્ય પરિમાણો આવશ્યક છે.
થ્રેડ સ્ટ્રિપિંગ અને સ્ક્રુ પુલ આઉટ સામે પ્રતિકાર માટે સ્ક્રુને સંબંધિત બોરનું કદ જટિલ છે.
થ્રેડની રચનાને કારણે હૂપના તાણનો સામનો કરવા માટે બોસનો બાહ્ય વ્યાસ એટલો મોટો હોવો જોઈએ.
ટૂંકી લંબાઈ માટે પ્રવેશના સમયે બોર થોડો મોટો વ્યાસ ધરાવે છે. આ ડ્રાઇવિંગ કરતા પહેલા સ્ક્રુ શોધવામાં મદદ કરે છે. તે બોસના ખુલ્લા અંતમાં તનાવને પણ ઘટાડે છે.
પોલિમર ઉત્પાદકો તેમની સામગ્રી માટે બોસનું પરિમાણ નક્કી કરવા માટે માર્ગદર્શિકા આપે છે. સ્ક્રુ ઉત્પાદકો સ્ક્રુ માટે યોગ્ય બોરના કદ માટે માર્ગદર્શિકા પણ આપે છે.
બોસમાં સ્ક્રુ બોરની આસપાસ વેલ્ડ સાંધાની ખાતરી કરવા માટે કાળજી લેવી જોઈએ.
બોસમાં મોલ્ડ-ઇન-સ્ટ્રેસ ન આવે તેની કાળજી લેવી જોઈએ કારણ કે તે આક્રમક વાતાવરણ હેઠળ નિષ્ફળ થઈ શકે છે.
બોસમાં બોર થ્રેડની thanંડાઈ કરતા વધુ shouldંડા હોવા જોઈએ.
10. સપાટીની સજાવટ
કેટલીકવાર, સારા દેખાવ માટે, અમે ઘણીવાર પ્લાસ્ટિકના કેસની સપાટી પર વિશેષ સારવાર કરીશું.
જેમ કે: ટેક્સચર, ઉચ્ચ ચળકતા, સ્પ્રે પેઇન્ટિંગ, લેસર એન્ગ્રેવિંગ, હોટ સ્ટેમ્પિંગ, ઇલેક્ટ્રોપ્લેટિંગ અને તેથી વધુ. પ્રોડક્ટની ડિઝાઇનમાં અગાઉથી ધ્યાનમાં લેવું જરૂરી છે, ત્યારબાદની પ્રક્રિયા પ્રાપ્ત કરી શકાતી નથી અથવા કદના ફેરફારોને ઉત્પાદન એસેમ્બલીને અસર કરે છે તે ટાળવા માટે.